Biesse Akron 440 AX
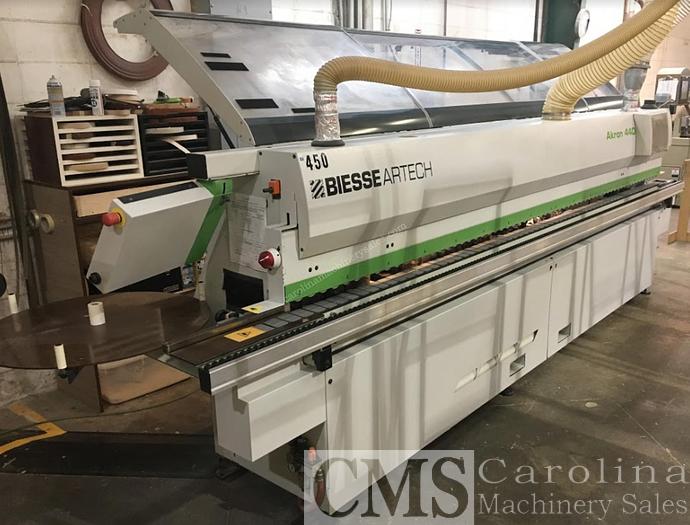
Specifications
Manufacturer | Biesse |
Model | Akron 440 AX |
Year | 2009 |
Stock Number | 007527 |
Voltage | 230V, 60Hz, 3Ph |
Description
This bander is in good running condition and ready to be loaded. TECHNICAL CHARACTERISTICS AKRON 440 AX “STANDARD” Panel thickness from 10 to 60 mm Height of edge-banding material from 14 to 64 mm Thickness of edge-banding material in rolls from 0,4 to 3 mm Thickness of edge-banding in strips from 0,4 to 8 mm Panel protrusion from track 25 mm Min panel length 140 mm Min panel width (with length 140 mm) 85 mm Min panel width (with length 250 mm) 50 mm Track feed speed 13 m/min Centralized dust extraction for operating units 1 hood Ø 150 mm Dust extraction system for edge-scraper unit 1 hood Ø 100 mm Dust extraction system for Pre-Mill unit 1 hood Ø 80mm Pneumatic connection 7 bar Working voltage 220 – 440 / 60 Hz three phase Control voltage 24 V - DC Static frequency inverter 200 Hz Glue pot capacity 2 Kg (approx) Glue pot heating time at ½ load 10 minutes (approx.) AKRON 440 AX with 6” Touch Screen Controller The AKRON 440 AX is a “Quick-Change” single sided edgebanding machine machine with Multi Profile type tooling for the application and processing of flat edgebanding material in coils (melamine, PVC, ABS, veneer) and in strip form (solid wood, Formica, planed veneers etc.). Innovative technology, NC controlled pneumatic logic, solid operating work units and heavy duty construction are combined to ensure a high quality finish and great reliability under a wide range of working conditions . STANDARD FEATURES 6” Touch Screen Numeric Control switch board The Numeric control TS06 manage the machine and its functions. Technical characteristics 6” graphic touch screen LCD display, 320x240 pixel. Glue Temperature control and auto temp kick-down WINDOWS CE Operating System USB port Auto “On & Off” of work units and work unit selections Automatic start-up of the units and motors foreseen by the programs. Button for direct selection of 2 nd run without the need to access the menu. Managing of 8 numeric axis. Lists of programs with manual and/or automatic start-up. Error diagnostics with codes and comments. Production statistics. The device is installed on an adjustable overhead control panel STRUCTURAL COMPONENTS Base I-BEAM FRAME provides the whole machine and work units, with stability and strength to allow precise, accurate machining. Integrated automatic chip removal system along the whole machine. Panel movement provided by a conveyor large industrial track pads and heavy duty Top pressure beam, combining a system that ensures optimum hold-down of the panel being processed, straight movement and resistance to side loads resulting from the forces when applying the edges. The conveyor Track utilizes an industrial chain with a 31.75 mm ( 1 ¼”) ratio, with track pads made from a special self-lubricating techno-polymer. The Track pads slide on two hardened steel guides, one with a circular section and the other one flat , complete with grease fittings for easy maintenance. The panels being edged are held by special low wear rubber pads with a high friction coefficient, which are individually interchangeable with a quick change system. (Pad dimensions are 80x60 mm). Main Gear motor for feed chain . Working speed 13 meter/min 1.5 kW motor. 4000204 NC Controlled / Motorized Top Pressure Beam The Heavy duty Top presser beam, with high rigidity, allows the constant change of the panel thickness without any manual set-ups or interventions on the operating units. The panels being edged are held in position by a double row of rubber staggered wheels with 32mm center to center spacing and mounted on precision bearings. The top working units are attached to the top presser and adjust automatically with the positioning of the top pressure beam itself. The top pressure beam movement is a centralized, with manual positioning via hardened steel guides and bushings. Lateral sliding panel support on bearings . It includes extruded aluminium guide complete of support wheels. Quick manual positioning and locking system. 4000207 Full protection safety hood with LIGHTS covers the entire length of the machine. It is made of extruded aluminium frame work with wide open surfaces in transparent polycarbonate for the complete view of the operating units. Centralized dust extraction connection. (150mm) E4000220 Increased Motor Power FROM 3,4 kW on E4000055 AKRON 440 AX WORKING UNITS PRE-MILLING UNIT FI-502 The Pre-Milling unit is utilized to clean the surface of the panel to be to be edged. The use of this unit insures a Clean / Flat even surface which will ensure a Clean / Tight thin glue spread. Also utilizing this unit will ensure a chip free finish thanks to; Horizontal and Vertical movement on Linear STAR guides Independent automatic “jump in & out” of the two cutter heads Independent copy shoe system Unit is complete with 3 mechanical high precision mechanical digital indicators and adjustments. 4000226 Dual DIAMOND coated cutter heads are 80mm x 65mm with a 3+3 tool pattern . Motor power of the unit is 3,5 KW GLUING, EDGE FEEDING AND PRESSING UNIT VC-511 Applies the hot melt glue onto the panel, feeds the edge to be applied to the panel being machined, automatically cuts the rolls of edge-banding material to length and presses the applied edge ensuring that it adheres perfectly to the panel. The system includes VC-511R Glue reservoir and glue spreading roller. The spreading roller is complete with a copying system to apply the correct amount of glue to the panel. The manual glue spread adjustment (dual position) for quick change. Manual device for the quick exclusion of the glue reservoir. No adjustment required when the panel thickness changes. Quick heating and double thermostat control for proper temperature control. The glue reservoir is completely coated with non-adhesive material for ease of maintenance. Automatic glue temperature lowering in the glue reservoir when the machine has been idle for a set period of time. Glue roller application rotating in the same direction of the panel feed. Quick change of the glue reservoir for an easy maintenance or color change / type of glue. Automatic Edge feeding system for edges in coils and for edges in strips, complete with roll holder disk diameter Ø 800 mm. The edge magazine table has a manual vertical adjustments for ease of set-up. Coil guillotine knife for the automatic cutting of edge-banding material in coils with a maximum thickness of 3 mm and with a maximum section of 140 mm 2 . Manual and fast adjustment of working pressure according to the thickness of edge-banding material being used. The guillotine is positioned prior to the 1 st main edge pressing roller. Edge pressure system “RPT” consisting of First main driven roller, diameter Ø100 mm, with independent pneumatic pressure adjustment. 2 idle rollers, diameter Ø60 mm, coated with non-adhesive material with pneumatic adjustment; they are opposing conical cones. 4000251 “RPT” – Edge pressure rollers with temporized intervention It does not require adjustment when changing the thickness of the edge to be applied and its thickness is between 0,4 and 3 mm (Over 3mm to 8mm solid lumber strips requires Digital manual adjustment) END TRIMMING UNIT / Pneumatic Tilting on PRISMATIC GUIDES IN-501V ( 2 motors 0,5kW each) HSD Electro Spindle Motors. Carries out the trimming on the ends of the panels to remove excess at the front and rear portion of the panel. E4000280 The cut can be accomplished straight (flush) or tilted (bevel) with a cutting angle between 0 and 15 degrees the cutting angle via Pneumatic tilting from the control panel. Degree displayed on a scale. Great reliability and precision due to the sliding on large prismatic Linear guides and heavy duty precision sliding bearing blocks. Fast tilting of the motors from 0 to 15 degrees Working exclusion from control board. Equipped with 2 high frequency motors (0,5 kW each) at 12.000 rpm complete with carbide tip saw blades. 4000102 TILTING top and bottom trimming UNIT RI-501 HSD Electro Spindle Motors. Carries out top and bottom trimming or fine finishing of edges, complete with front and vertical rotating self-cleaning disk copiers.(Copy wheels) The unit can be manually tilted from 0 to 25 degrees using the UNIPOINT system. Made from a single, monolithic, high-rigidity structure bolted to the I-Beam frame to ensure precise machining. The top unit is self-adjusting according to panel height. Main horizontal and vertical slides are on hardened steel rods with Linear bushings. 4000300 Pneumatic exclusion of unit code Motors 12000 rpm complete with suction hoods. Tools ø 70 x 20 x 16 with disposable inserts / Straight knives. 4000340 MULTIFUNCTION 2 MOTORS CORNER ROUNDING UNIT CR-200V - 2 motors 0,65 4000346 kW each with cutters R=3mm The unit carries out the CORNER ROUNDING and the TOP AND BOTTOM TRIMMING on panels edged with synthetic material up to max. edge thickness of 3 mm. The CORNER ROUNDING processing is possible both on panels with straight profiles and standard post-soft formed panels with 90 and 180 degrees. High finishing quality thanks to movement on linear guides with recirculating ball screws, vertical oscillating copying system, frontal copying device with PRE-COPYING system. 4000343 Quick and reliable changeover (doesn't require any manual intervention) between thin and thick edges (i.e. between 0,4 mm TO 3mm) with system FAST consisting of 4 positions that can be pre-selected Via PLC controlled / 3 positions of BEVEL CUT and 1 position of Radius cut. Equipped with R=3 mm braze-welded. 2 high frequency motors 12000 rpm. Complete with pneumatic exclusion from Control board. 4000103 EDGE SCRAPER RBK-502 Carries out finishing operations on thick PVC/ABS edge-banding coils or strips. Solid steel structure for precise, safe machining. Complete with vertical and horizontal rotating copying wheels. Fast, easy adjustment thanks to 4 mechanical numerical digital indicators. Standard accessories include compressed air blowers on the copiers. E4000360 Pneumatic exclusion of the unit from the control panel E4000361 Unit complete with dust extraction (PVC shavings) container. E4000362 Complete with interchangeable knife blades R=3mm . 4000104 GLUE-SCRAPER RCC-701 Auto-aligning with the panel surface and auto-adjusting with the thickness to remove the exceeding glue in the junction EDGE TO PANEL.. Complete with copy wheel system copying device and flat blade knifes. Unit includes as standard ï Pneumatic exclusion. ï Timed intervention of the flat knifes. ï Air blowers with nebulised liquid for the cleansing of the knives. E4000105 BRUSHING UNIT SP-501 To carry out the cleaning and polishing of the applied edge using cloth disc brushes. The unit is tiltable and Self-adjusting to the panel height. It includes two 370 W motors at 2800 rpm. 4000106 HOT AIR BLOWER PH-501 To reactivate the color of thick ABS or PVC Edges (i.e. 2 or 3 mm pvc/abs) after the Profile scraping operation. Machine equipped with a single hot air blower, 2000 W , with adjustable temperature control.