2013 Butfering Profi SWT-345 Sander
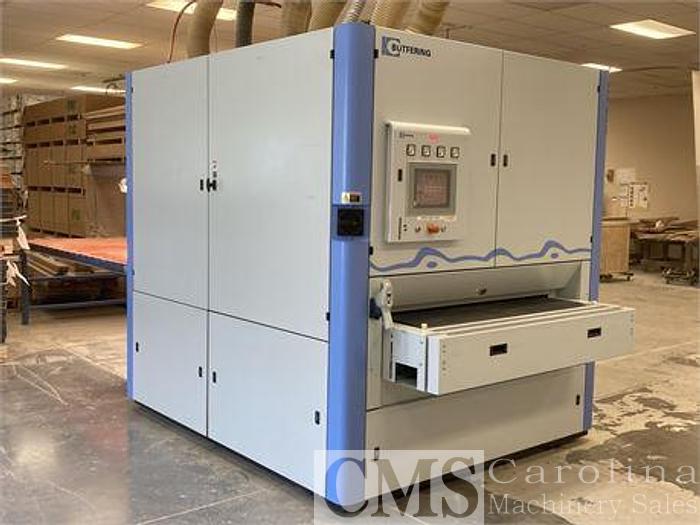
Specifications
Manufacturer | Butfering |
Model | Profi SWT-345 Sander |
Year | 2013 |
Stock Number | 009311 |
Description
Butfering Model Profi SWT-345/QHQQ
Butfering's SWT 345 QHQQ is designed to sand lacquered and veneered work-pieces. Equipped with four (4) sanding units and MPS 25 segmented sanding pads, the SWT 345 QHQQ is a versatile production solution when veneer sanding and short grain sanding is required.
Butfering's SWT 300 series includes the following features:
- constant pass-line, 35" (900 mm)
- protected storage space for spare sanding inserts
- automatic "Star Delta" starting
- maintenance-free electrical main motor braking
- electronic abrasive belt oscillation
- pneumatic tensioning of abrasive belt
- abrasive belt edge compensation
- safety switch-off of machine during faulty operation
- rubberized pressure rollers
- automatic head locking
1/8" - 6" workpiece thickness
53" working width
54" x 103" abrasive belt size
Equipped with work-piece sensing with 25 mm resolution for the Magnetic Pad System
Variable frequency-controlled feed speeds of 2.5 – 13 m/min. (8 – 42 FPM)
Telescopic work-piece feeding roller table on infeed
Vacuum table feedbelt
4.7 HP fan motor
650 CFM
TE-14 Controller with touch screen
10.4" color screen
Millimeter or inch readout
Pre-set activation allows the operator to change the program while the machine is currently running another program. When the current part clears the machine, the new program will activate.
Wireless thickness caliper, 0" - 2". Transmits the work piece thickness to the machine controller automatically when the send button is pressed.
Unit 1
Q-Head – Cross sanding unit
This cross sanding head runs perpendicular to the belt feed. It is ideal for white wood sanding of laid up veneer panels as it levels out the veneer joints and aids in reducing wood fiber length. The cross belt is also used for sealer / lacquer sanding as well as sanding high gloss materials. 5360 x 150 mm (233" x 6") abrasive belt length.
18 HP motor
6.6 - 52.5 F/Sec. sanding speed
MPS-25 Magnetic controlled segmented pad with electro-magnetically controlled pressure.
Unit 2
H-Head – Longitudinal sanding with Inner Chevron Belt
Longitudinal sanding head with a segmented pressure pad and Inner Chevron Belt
30 HP motor
6.6 - 52.5 F/Sec. sanding speed
MPS-25 Magnetic controlled segmented pad with electro-magnetically controlled pressure.
Air jet blower with five (5) settings
Unit 3
Q-Head – Cross sanding unit
This cross sanding head runs perpendicular to the belt feed. It is ideal for white wood sanding of laid up veneer panels as it levels out the veneer joints and aids in reducing wood fiber length. The cross belt is also used for sealer / lacquer sanding as well as sanding high gloss materials.
6" x 233" abrasive belt size
18 HP motor
6.6 - 52.5 F/Sec. sanding speed
MPS-25 Magnetic controlled segmented pad with electro-magnetically controlled pressure.
Unit 4
Q-Head – Cross sanding unit
This cross sanding head runs perpendicular to the belt feed. It is ideal for white wood sanding of laid up veneer panels as it levels out the veneer joints and aids in reducing wood fiber length. The cross belt is also used for sealer / lacquer sanding as well as sanding high gloss materials.
6" x 233" abrasive belt size
18 HP motor
6.6 - 52.5 F/Sec. sanding speed
MPS-25 Magnetic controlled segmented pad with electro-magnetically controlled pressure.
Rotary Air Jet Work Piece Cleaning with De-ionization
Butfering's Integrated Cleaning Plant includes a de-ionization bar to reduce static charge for better work-piece cleaning. The cleaning plant also includes a work-piece cleaning device with rotating air jets.
Roller Out Feed Table
A roller table at the out feed assists in transporting work-pieces from the machine and features an extension of 300 mm (11.8").
Outfeed conveyor NOT included
Listed specifications were taken from manufacturer's published information and is assumed to be correct but not guaranteed. Bidder is encouraged to inspect the machine, call with questions or contact the manufacturer for more information.